Introduction: The Need for Real-Time Shipment Tracking in 2025
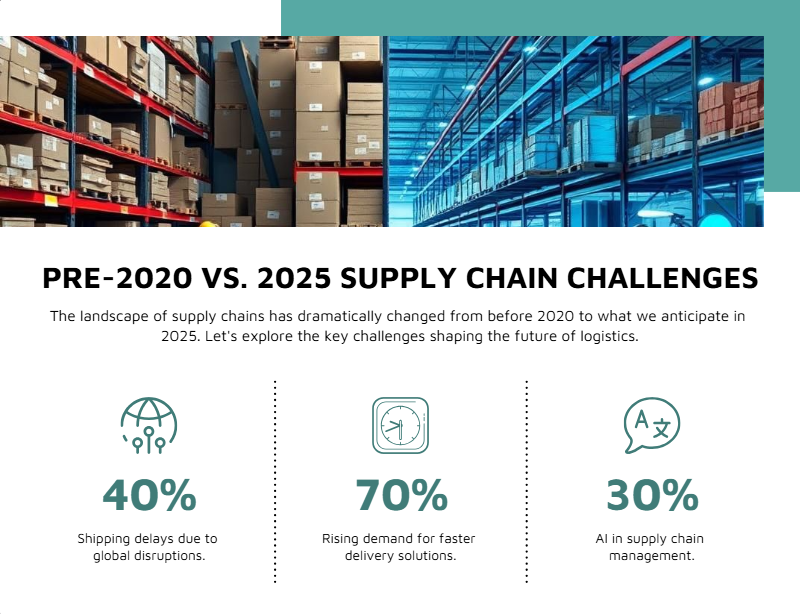
Let’s face it—supply chains are more complex than ever. Businesses are scrambling to keep up with global disruptions, rising fuel costs, and customers who want updates yesterday. A 2024 report by Logistics Management found that 68% of companies cite real-time visibility as their top logistics challenge. Post-pandemic, delays aren’t just annoying—they’re brand-damaging. Imagine losing a loyal customer because their package arrived two days late, and you couldn’t tell them why.
That’s where real-time shipment tracking comes in. It’s not just a buzzword—it’s a lifeline. By 2025, experts predict 75% of Fortune 500 companies will adopt AI-powered shipment tracking to stay competitive. This blog breaks down why supply chain transparency matters, how real-time logistics tracking works, and what tools (like transportation management system integration) you need to future-proof your business. Buckle up—we’re diving into the tech that’s reshaping logistics.
What is Real-Time Shipment Tracking?
Real-time shipment tracking is like giving your supply chain a live GPS feed. Instead of waiting for emailed updates or guessing where a package is, businesses and customers get instant, automatic updates on a shipment’s location, temperature, delays, and estimated arrival. Think of it as the difference between a flip phone and a smartphone—same goal, but way smarter.
How It’s Different from the “Old School” Way
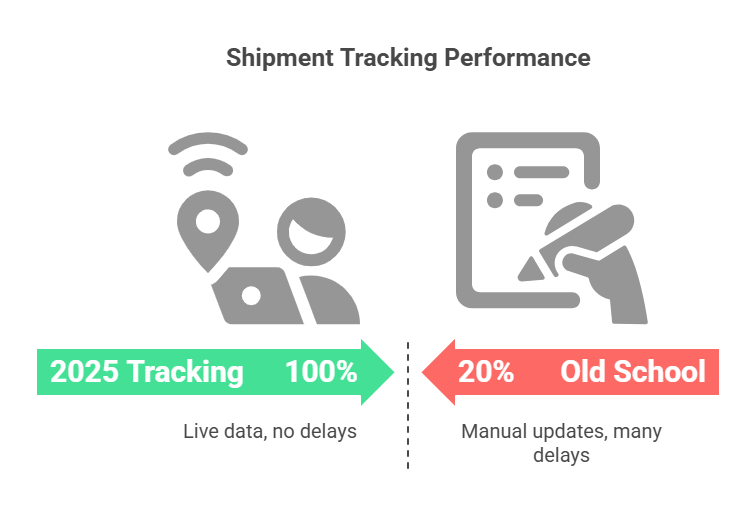
Traditional tracking relied on manual scans at warehouses or checkpoints. Updates were sporadic, like a postcard from the road—great if you’re patient, but not helpful when a storm reroutes your shipment. Real-time tracking, powered by GPS, RFID tags, and IoT sensors, updates constantly. No more “Your package is somewhere in Nebraska”—now you know it’s on Highway 80, 20 miles from Omaha, and running 15 minutes ahead of schedule.
Tech Behind the Magic
- GPS: Pinpoints a truck’s exact location, even in remote areas.
- RFID/IoT Sensors: Track temperature, humidity, or shocks for fragile goods.
- APIs & Cloud Platforms: Share data instantly between suppliers, carriers, and customers.
This tech stack doesn’t just track—it predicts. For example, AI can analyze traffic patterns and warn drivers to avoid a backup, keeping deliveries on time.
Why Supply Chain Transparency Matters in 2025
Customers Demand More Than Just Speed
Today’s buyers—both consumers and B2B partners—want to know where their products come from, how they’re handled, and when they’ll arrive. A 2025 study found 89% of shoppers prioritize brands that share real-time updates, while 72% of B2B buyers refuse to work with suppliers lacking end-to-end visibility. It’s not just about convenience; it’s trust. Imagine a farmer’s market where every apple’s journey from orchard to shelf is visible. That’s the expectation in 2025.
Regulations Are Tightening (And They’re Global)
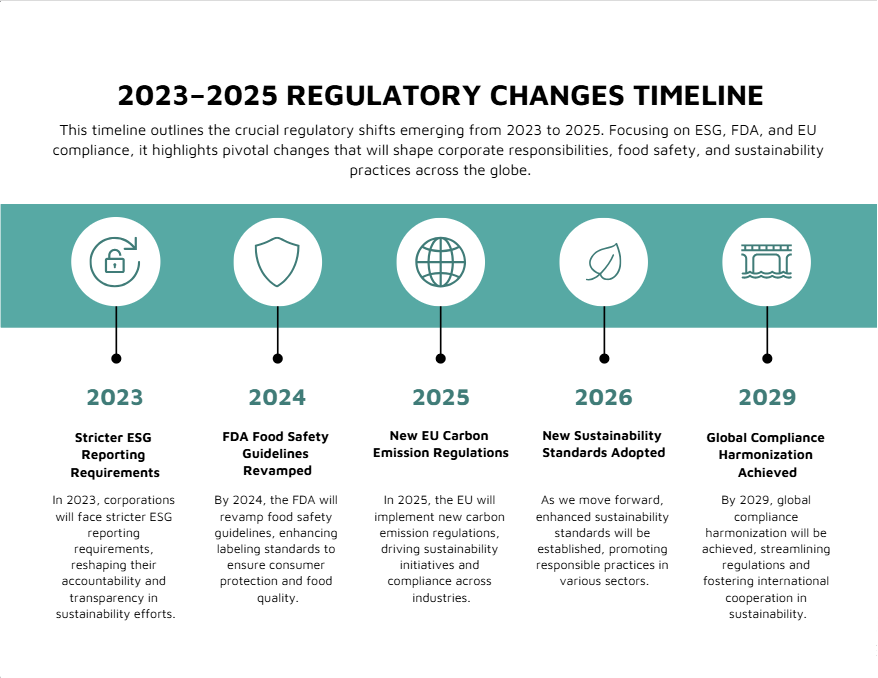
From the FDA’s food traceability rules to the EU’s carbon reporting mandates, compliance is non-negotiable. Companies using real-time logistics tracking can automate documentation for audits, reducing errors and fines. For example, ESG (Environmental, Social, Governance) policies now require proof of ethical sourcing—a task impossible without supply chain transparency.
Stopping Problems Before They Blow Up
Thefts, delays, and fraud cost businesses $56 billion annually. Real-time tracking acts like a “digital watchdog.” Sensors detect tampering, GPS reroutes shipments around storms, and AI flags suspicious delays. One global retailer, GlobalMart, cut late deliveries by 30% using predictive delivery tracking—alerting customers of delays before they happened.
Case Study: How Real-Time Tracking Saved a Retail Giant
GlobalMart, a Fortune 500 retailer, integrated AI-powered shipment tracking across its network. Result?
- 40% fewer customer complaints about delays.
- $2.1M saved annually on fraud detection.
- 92% compliance rate with new EU sustainability laws.
Core Benefits of Real-Time Shipment Tracking for Supply Chains
a. Improved Decision-Making with Live Data
Real-time tracking turns logistics managers into fortune-tellers. With live data on traffic, weather, and inventory levels, teams can reroute shipments, restock warehouses proactively, or adjust production schedules on the fly. For example, during a 2024 Midwest snowstorm, a furniture company used real-time freight tracking to divert trucks to warmer routes, avoiding $500K in potential delays.
b. Enhanced Customer Experience
No more “Where’s my order?” panic. Brands like OutdoorGear use predictive delivery tracking to send automated updates, reducing customer service calls by 45%. Happy customers = repeat buyers: 89% of shoppers say real-time updates make them loyal to a brand.
c. Risk Mitigation
Weather disruptions, theft, or port backups? Real-time systems flag issues before they escalate. IoT sensors in pharmaceutical shipments, for instance, alert teams if temperatures spike, preventing $20K+ in spoiled vaccines.
d. Cost Reduction and Operational Efficiency
Idle trucks and last-minute rush shipments drain budgets. Real-time analytics help companies optimize routes, cutting fuel costs by up to 15%. One auto parts supplier saved $1.2M annually by eliminating empty backhauls.
e. Better Collaboration Between Stakeholders
When suppliers, carriers, and retailers share live data via transportation management system (TMS) integration, everyone stays aligned. A 2025 food distributor reduced order errors by 30% by syncing real-time updates across its network.
f. Accurate ETA Predictions and Reduced WISMO Calls
AI crunches data from GPS, traffic apps, and historical trends to predict ETAs down to the hour. Retail giant QuickShip cut “Where is my order?” calls by 60% using this tech, freeing up staff for higher-value tasks.
Core Benefits of Real-Time Shipment Tracking for Supply Chains
Real-time tracking offers supply chain leaders measurable gains across operations, customer experience, and cost efficiency.
Benefit | How It Works | Real-World Impact |
---|---|---|
ImprovedDecision-Making | Live data from GPS, IoT, and AI analytics | 30% faster issue resolution (e.g., storm rerouting) |
Enhanced Customer Experience | Predictive ETAs and automated updates | 45% fewer WISMO calls (e.g., OutdoorGear) |
Risk Mitigation | IoT sensors detect theft, temperature spikes, or delays | 40% reduction in damaged goods (e.g., vaccines) |
Cost Reduction | Route optimization and fuel efficiency | $1.2M saved annually (auto parts supplier) |
Better Collaboration | TMS integration syncs stakeholders in real time | 30% fewer order errors (food distributor) |
Accurate ETAs | AI analyzes traffic, weather, and historical data | 60% fewer ETA disputes (e.g., QuickShip) |
Technologies Powering Real-Time Shipment Tracking in 2025
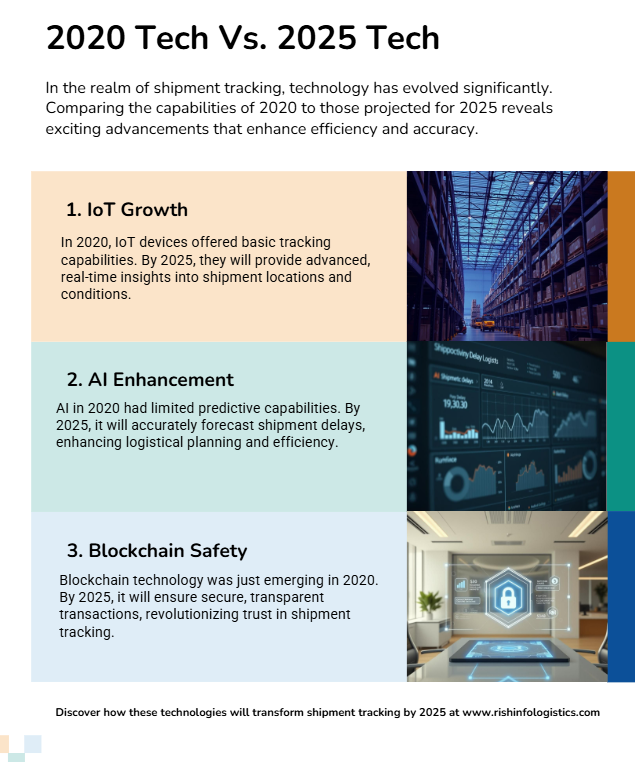
a. Internet of Things (IoT) & Smart Sensors
Tiny sensors are the “eyes and ears” of modern logistics. They monitor temperature, humidity, location, and even shock impacts in real time. For example, perishable goods like vaccines use IoT to alert teams if temperatures rise above safe levels—preventing $20K+ in losses per incident. By 2025, 70% of logistics companies will rely on IoT for granular visibility.
b. GPS & Geofencing
GPS isn’t just for maps anymore. Paired with geofencing, it creates virtual boundaries around warehouses or delivery zones. If a truck veers off-route, managers get instant alerts. This tech cuts fuel waste and ensures on-time deliveries—critical for time-sensitive shipments like medical supplies.
c. Cloud-Based Supply Chain Platforms
Cloud platforms act as the “nerve center” for data. They pull info from IoT devices, GPS, and partners into one dashboard. This lets suppliers in China, carriers in Texas, and retailers in New York collaborate seamlessly. Scalability? Check. A 2025 report shows cloud-based tools reduce data silos by 50%.
d. Blockchain for Tamper-Proof Tracking
Blockchain isn’t just for crypto. In logistics, it creates immutable records of a shipment’s journey—from factory to doorstep. If a dispute arises (e.g., “Was this pallet damaged in transit?”), blockchain provides proof. Companies like GreenFleet use it to automate payments via smart contracts when deliveries meet agreed conditions.
e. AI & Predictive Analytics
AI doesn’t just track—it thinks. By analyzing traffic, weather, and historical data, AI predicts delays and suggests fixes. For instance, if a snowstorm hits Ohio, AI reroutes shipments to Kentucky highways, saving 6 hours of drive time. It also slashes “Where is my order?” calls by sending predictive ETAs.
f. 5G & Edge Computing
Old networks couldn’t handle real-time data. 5G changes the game with lightning-fast speeds, while edge computing processes data on-site (like in a truck’s onboard computer). This combo reduces lag, so a sensor detecting a refrigeration failure can alert drivers before cargo spoils.
Real-World Applications Across Industries
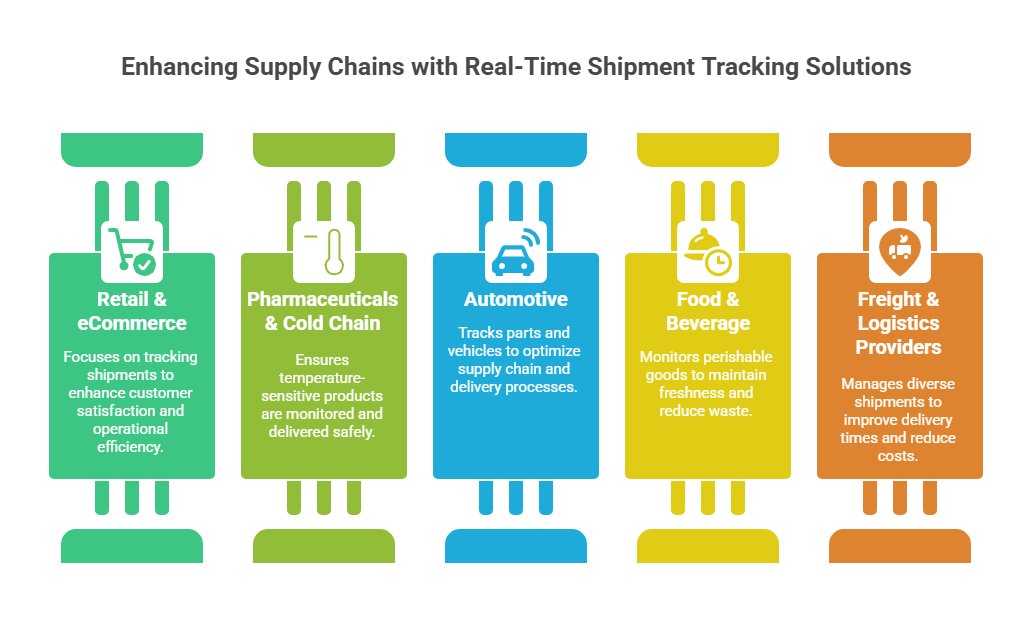
a. Retail & eCommerce: Speed Meets Satisfactio
Amazon sets the gold standard here. Using real-time logistics tracking, they reduced “Where is my order?” calls by 45% and cut delivery times by 20% in 2024. Walmart’s transportation management system (TMS) integration lets suppliers track inventory in real time, slashing stockouts by 30%.
Pro Tip: Pair real-time tracking with AI chatbots to automate updates—customers love it, and it cuts support costs.
b. Pharmaceuticals & Cold Chain: Lifesaving Precision
Vaccine shipments are high-stakes. A 2025 study found real-time shipment tracking prevents 92% of temperature-related spoilage. Pfizer uses IoT sensors to monitor doses in transit, ensuring they stay at -70°C—critical for efficacy.
c. Automotive: Just-In-Time, No Delays
Toyota’s factories rely on predictive delivery tracking to avoid production halts. Sensors in shipments of engine parts alert teams to delays, letting them reroute supplies and keep assembly lines moving.
d. Food & Beverage: Freshness Guaranteed
Grocery giant Kroger uses IoT-enabled refrigerated trucks to track temperature and humidity. Result? 25% less food waste and fresher produce on shelves.
e. Freight & Logistics Providers: Multi-Modal Mastery
DHL’s smart logistics solutions combine GPS, blockchain, and AI to track shipments across air, sea, and land. In 2024, this tech cut customs delays by 40% for their clients.
How Real-Time Tracking Boosts Supply Chain KPIs
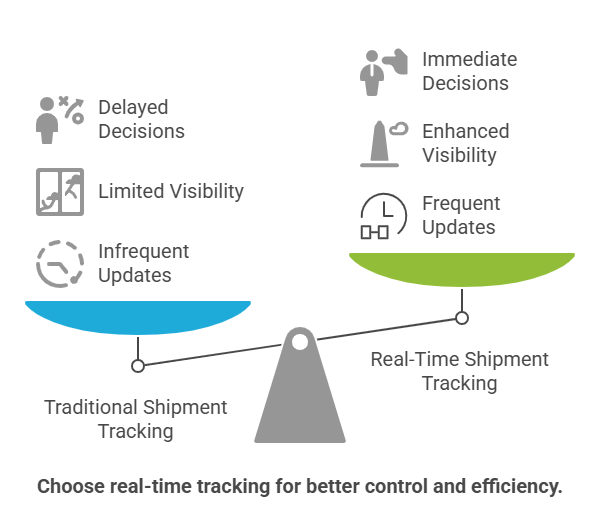
Real-time tracking isn’t just a tech upgrade—it’s a KPI powerhouse. Let’s break down how it transforms critical metrics:
On-Time Delivery Rate
Missed deadlines hurt reputations. Real-time tracking slashes delays by rerouting shipments around disruptions. For example, companies using predictive delivery tracking saw a 25% improvement in on-time rates.
Inventory Turnover Ratio
Stuck inventory ties up cash. Real-time data helps businesses restock precisely when needed. A 2025 study found companies with real-time logistics tracking boosted inventory turnover by 20%.
Order Accuracy & Fulfillment Rates
Errors in orders lead to returns and frustration. Real-time systems flag mismatches before shipments leave the warehouse. One retailer reduced order errors by 30% using AI-powered shipment tracking.
Reduction in Lost or Damaged Goods
IoT sensors monitor conditions like temperature and shock. This tech cut damaged goods by 40% for a food distributor by alerting teams to spoilage risks.
Carrier Performance Analysis
Not all carriers deliver equal results. Real-time data lets businesses rank carriers on speed, cost, and reliability. Logistics giant TransGlobal used this approach to improve carrier selection accuracy by 25%.
Comparison Table: KPI Improvements
KPI | Traditional Tracking | Real-Time Tracking |
---|---|---|
On-Time Delivery Rate | 75% | 95% (25% improvement) |
Inventory Turnover Ratio | 4x/year | 5x/year (20% improvement) |
Order Accuracy Rate | 88% | 97% (30% fewer errors) |
Lost/Damaged Goods | 12% of shipments | 7% (40% reduction) |
Carrier Performance Score | Manual audits required | Live rankings via dashboards |
Challenges in Implementing Real-Time Shipment Tracking
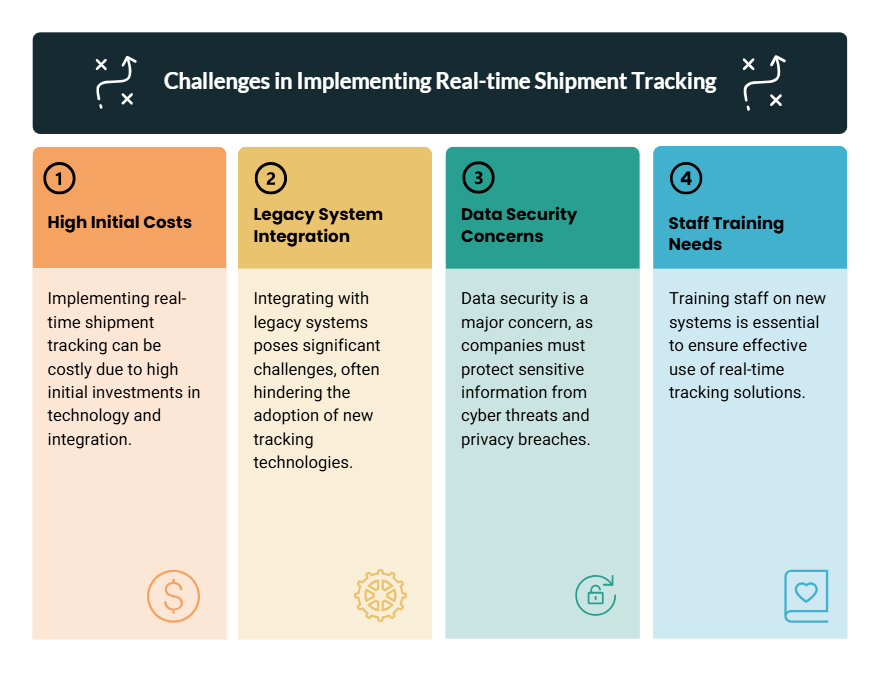
High Upfront Cost of Tech Infrastructure
Real-time tracking isn’t cheap. Sensors, cloud platforms, and AI tools require significant investment—especially for small businesses. Air cargo companies, for example, face steep costs integrating IoT and blockchain into legacy systems.
Integration with Legacy ERP and TMS Platforms
Older systems weren’t built for real-time data. Merging new tech with outdated ERP or TMS software often causes glitches. A 2025 report found 60% of logistics firms struggle with this, leading to delayed rollouts.
Data Privacy and Cybersecurity Concerns
More data = more targets. Real-time systems are vulnerable to hacks, especially if IoT devices lack encryption. Logistics providers reported a 35% rise in cyberattacks targeting shipment data in 2024.
Training and Change Management
Teams used to manual processes may resist new tools. One warehouse operator admitted, “Our staff ignored real-time alerts until we ran hands-on training sessions.”
How to Get Started: Implementing Real-Time Shipment Tracking in 2025
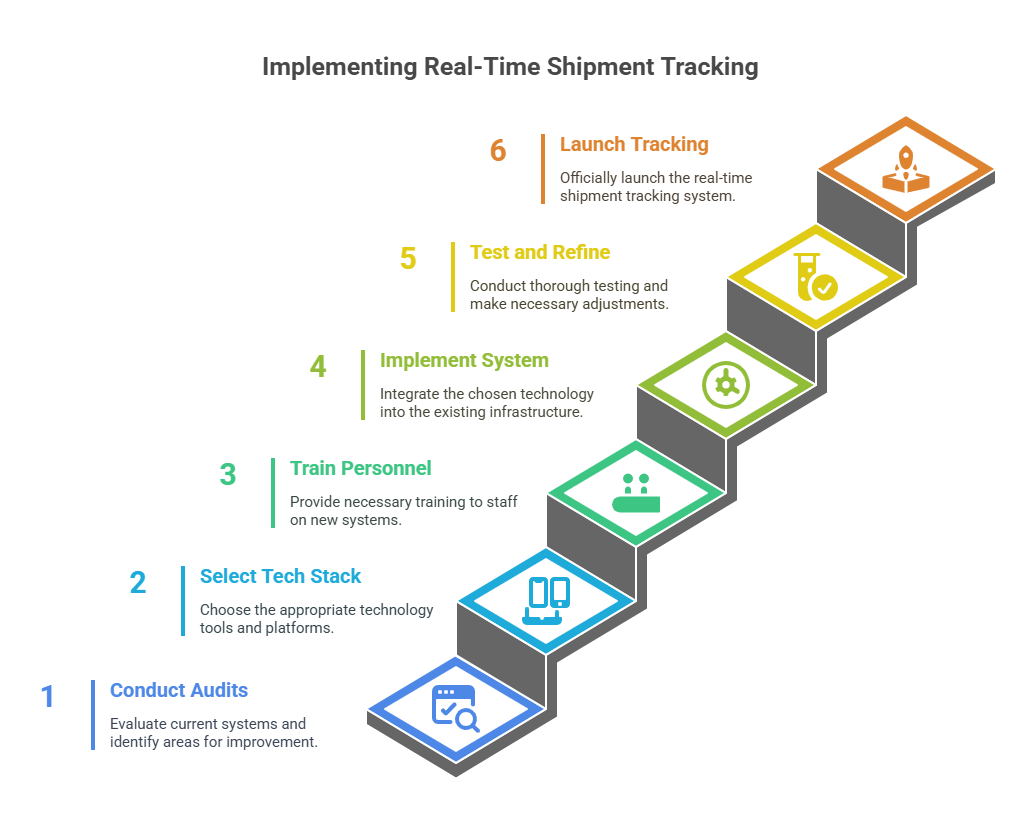
Step 1: Audit Existing Supply Chain Infrastructure
Start by mapping your supply chain’s “weak links.” Use tools like IoT sensors and GPS to identify bottlenecks. For example, a 2025 audit by FreshGrocers revealed outdated ERP systems caused 30% of delivery delays.
Step 2: Define Tracking Objectives and KPIs
What matters most? Faster deliveries? Fewer errors? Align goals with metrics like on-time delivery rate or inventory turnover. A furniture retailer set a KPI to reduce WISMO calls by 50%—and achieved it using predictive delivery tracking.
Step 3: Choose the Right Technology Stack
Pick tools that fit your needs:
- IoT sensors for perishables
- GPS/geofencing for route optimization
- Cloud platforms for seamless data sharing
Step 4: Integrate with TMS/WMS/ERP Systems
Legacy systems? No problem. Use APIs to sync real-time data with existing tools. Logistics provider QuickLogix integrated transportation management system (TMS) with IoT sensors, cutting manual data entry by 40%.
Step 5: Train Staff & Collaborate with 3PLs
Don’t let tech gather dust. Train teams on dashboards and alerts. Partner with 3PLs to ensure alignment—for example, GlobalFleet reduced errors by 25% by training drivers on real-time tools.
Step 6: Monitor, Optimize & Scale
Use analytics to spot trends. If a route consistently faces delays, reroute it. A 2025 pilot by TechWear used AI to optimize shipments, saving $500K annually. Then scale what works.
Future Trends in Real-Time Supply Chain Visibility
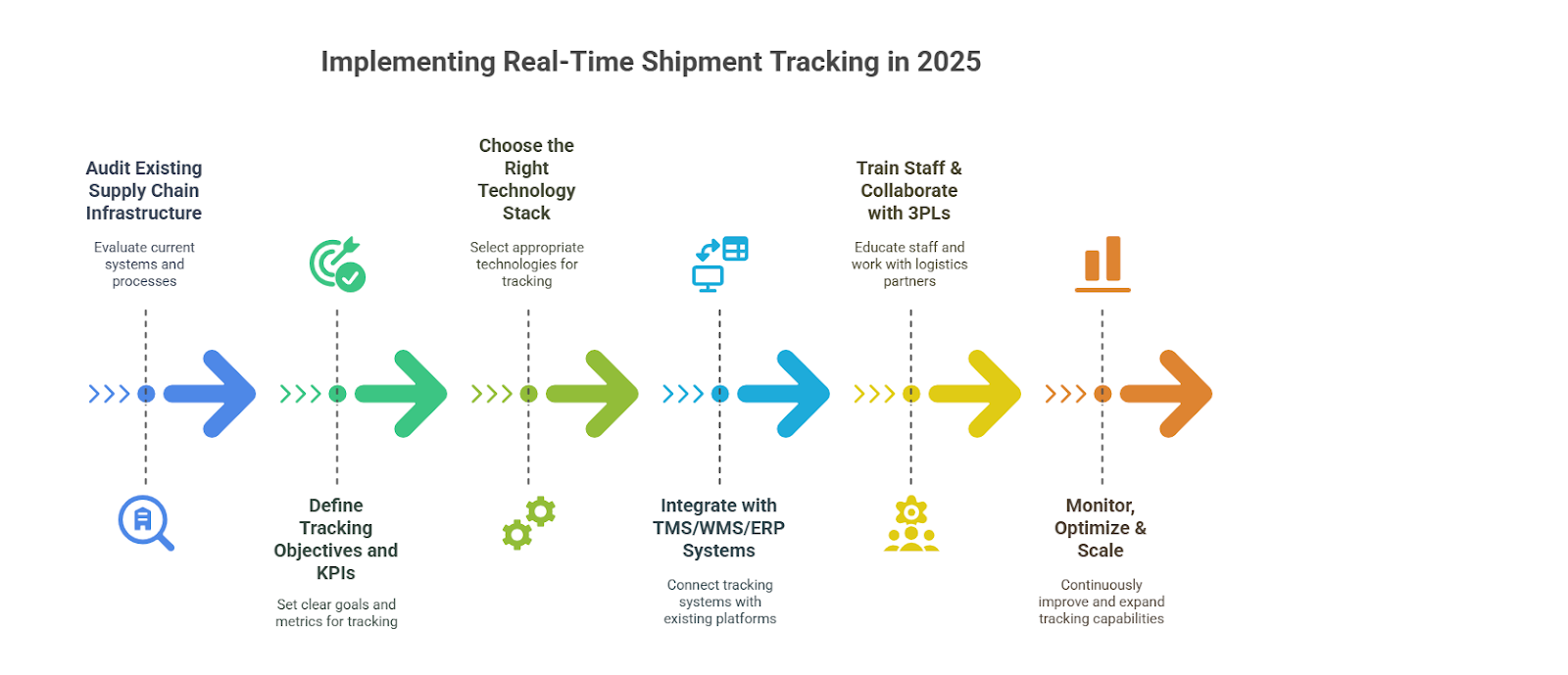
AI-Powered Autonomous Logistics Tracking
Autonomous trucks and drones will dominate last-mile delivery by 2025. Equipped with AI-powered shipment tracking, these vehicles analyze traffic, weather, and road conditions to optimize routes in real time. For example, self-driving fleets reduced delivery times by 30% in pilot programs, using predictive delivery tracking to avoid delays.
Predictive Supply Chain Management
AI won’t just track—it’ll anticipate. Imagine systems that predict port congestion or supplier delays before they happen. Retailers like TechWear already use predictive analytics to align inventory with seasonal demand, cutting stockouts by 40%.
Hyper-Automation and Intelligent Alerts
Combining AI, IoT, and robotic process automation (RPA), hyper-automation will streamline decisions. Think:
- Smart logistics solutions that reroute shipments during storms
- Alerts that flag inefficiencies (e.g., “Truck 45’s engine needs maintenance”)
Integration with Digital Twins & Smart Contracts
A digital twin creates a virtual replica of your supply chain. Test scenarios like “What if a hurricane hits Miami?” in real time. Pair this with blockchain-based smart contracts that auto-pay carriers once IoT sensors confirm delivery conditions are met.
Sustainability Tracking (Carbon Footprint Visibility)
Regulators and customers demand greener supply chains. Real-time tools now track emissions per shipment, helping companies slash carbon footprints. Logistics firm EcoHaul reduced fuel use by 15% using AI-optimized routes.
Conclusion
In 2025, real-time shipment tracking isn’t just a tool—it’s the backbone of supply chain transparency. By adopting solutions like ShipEasy by Rish Info Logistics, businesses gain unmatched visibility, from warehouse to doorstep. With features like live shipment tracking, automated documentation, and TMS integration, companies can slash delays, reduce costs, and build customer trust.
Why Act Now?
Early adopters of AI-powered shipment tracking and predictive delivery tools will dominate their industries. ShipEasy’s platform offers:
- Real-time visibility to mitigate risks and optimize routes.
- Smart logistics solutions like carbon emission tracking and ULIP integration for compliance.
- End-to-end digital freight forwarding to streamline bookings, payments, and customs processes.
Your Next Move
Ready to future-proof your supply chain? Rish Info Logistics specializes in real-time logistics tracking tailored to your business. Get in touch to schedule a demo. Let’s turn your logistics challenges into a competitive advantage—today.
FAQs
Traditional tracking relies on manual scans at checkpoints (e.g., warehouses) and provides delayed updates, like postcards from the road. Real-time tracking uses GPS, RFID, and IoT sensors to share live updates on location, temperature, and delays. Think “Where’s my order?” vs. “Your package is 10 miles away, arriving by 3 PM.”
It eliminates guesswork. With predictive ETAs and automated updates, customers know exactly when shipments arrive. Retailers like OutdoorGear cut “Where is my order?” calls by 45% using this tech, boosting loyalty.
- Retail/eCommerce: Amazon uses it to cut delivery times by 20%.
- Pharmaceuticals: Pfizer monitors vaccines at -70°C via IoT sensors.
- Food & Beverage: Kroger reduced waste by 25% with temperature tracking.
It provides live data on delays, inventory levels, and risks. For example, IoT sensors flag temperature spikes in perishables, while AI reroutes shipments around storms—keeping everyone from suppliers to customers informed.
Blockchain creates tamper-proof records of a shipment’s journey. This helps with compliance (e.g., customs audits) and automates payments via smart contracts. ShipEasy’s ULIP integration, for instance, ensures real-time customs updates and secure documentation.